API 610 is a set of standards written and regulated by the American Petroleum Institute to ensure that reliability and safety standards are upheld in what can be a dangerous industry. This regulation focuses on the minimum requirements for centrifugal pumps in the chemical, petroleum and gas industries regarding safety, maintainability and reliability.
The standards cover all centrifugal pump packages—horizontal and vertical pumps, single- and two-stage pumps, multistage pumps, single- and double-case pumps, vertical sump, vertical canned, and others that are found in the oil and gas industry. API 610 pumps are used in many areas—offshore oil rigs, onshore oil production facilities, oil refineries, chemical and gas processing plants, and power stations.
Design
The safety of a pump system in the oil and gas industry is extremely important. Therefore, the stringent requirements of all components involved must be considered during the design process. If care is not taken in selecting and designing these pumps, catastrophic failures can occur.
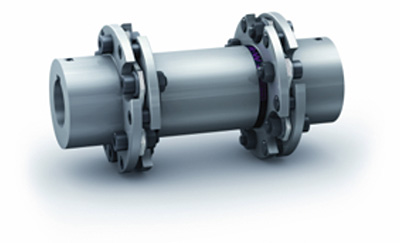
The reliability of the system is also important. API 610 pump packages are designed for a minimum service life of 20 years and at least three years of uninterrupted service. Downtime can cost the operators millions per day, making the selection of all components involved important. From a maintenance standpoint, many requirements in place allow for a quick and simple overhaul of an entire system.
Coupling Selection
These requirements hold true when selecting the coupling that will be used in an API 610 package. The couplings should be safe, reliable and maintenance-friendly, and certain standards are set for them. Specific standards are set for a coupling that will be used in an API 610 pump package.
An API 610 coupling is an all-metal, flexible element spacer coupling in accordance with American Gear Manufacturer Association (AGMA) 9000, Class 9 standards for balance quality to reduce vibration. Balancing in accordance with the International Organization for Standardization (ISO) 40441 must be met if operating at speeds in excess of 3,800 rpm. The coupling must include corrosion-resistant, flexible elements with steel hubs. The design must also include a safety catch to retain the spacer if one of the flexible elements ruptures unexpectedly. The nominal length of the center spacer should be at least 5 inches long to allow for removal of the coupling, seal, bearing(s) and rotor without disturbing the motor or adjacent pump components.
Additional requirements are set beyond these key characteristics, and they all ensure that a highly reliable and easy-to-use coupling will be installed, making the sizing and selection of the flexible coupling in an API pump package an important undertaking.
Designed to protect drive shafting, bearings and gears from stress-related changes to misalignment and structural changes, a flexible shaft coupling is subject to many bending cycles during its life. More traditional designs require either periodic lubrication or replacement of wear parts to help relieve the stress.
Frequent maintenance is unacceptable in these critical installations. Metallic flexible couplings are typically designed to fully eliminate wear based on the principle of fatigue resistance. Material fatigue results from a certain number of stress cycles at a certain stress amplitude. In a flexible coupling, this essentially means the number of shaft rotations at certain levels of misalignment and torque.
For ferrous materials, when the stress amplitude is known and kept below the fatigue limits of the flexible element in the coupling (the misalignment and torque ratings), any number of cycles can be tolerated without fatigue. The goal is infinite product life.
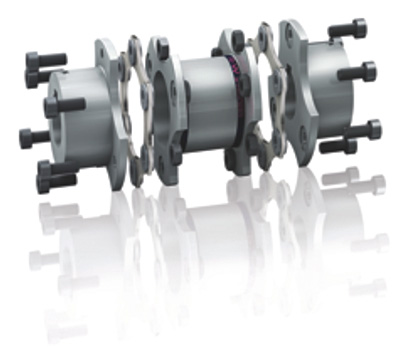
Disc Pack Couplings
A coupling manufacturer produced a line of wear-free disc pack couplings to meet the API 610 requirements for centrifugal pump packages. These API-610-compliant disc pack couplings are designed to be reliable and wear and maintenance free. The company’s engineers intended to improve the existing methodology.
These disc pack couplings are different because they transmit torque across the disc pack assemblies purely by friction to avoid problems associated with stress concentration, backlash and micro-movements—all of which can result from transmitting torque across the shanks of shoulder bolts. A series of bushings are pressed together to assemble the disc packs, while precision locating features in the hubs and spacers present a concentric fit. The bolt assemblies are then tightened through the hubs, spacers and bushings to generate the necessary clamping pressure across the faces of the disc packs to transmit all the power by friction. The frictional connection of the disc packs further increases service life and makes the complete coupling assembly more torsionally stiff.
Two precision-machined coupling hubs and a precision spacer tube made from steel are mounted to the corrosion resistant disc packs with high-strength screws and bushings for alignment and frictional clamping of the complete assembly. Integral safety catches are in place to retain the spacer in the event of an unexpected disc pack rupture. The center spacer can be easily removed for maintenance of components—such as seals and rotors—without disturbing the adjacent equipment.
These disc pack couplings meet all the balancing requirements set by the API 610 guidelines, and ISO 1940-1 grade G6.3 balancing is also available. They can be customized with features to meet the end user’s specific needs, such as adding puller holes for interference fit connections and large hub design for oversized bores. A team of engineers at the coupling manufacturer developed these wear-free disc pack couplings to address challenging application requirements and API 610 standards.