Eccentric disc technology has been successfully used as a solution in pumping applications for decades. One specific eccentric disc pump style that was introduced in 1965 has sold tens of thousands of units in Western Europe alone. Many of these units have provided 30 to 40 years of service with virtually no maintenance.
Eccentric disc pump technology was originally tailored specifically for the Western European oil and chemical markets because of its unique design. This design enables the pump to transfer viscous, non-lubricating, volatile and delicate materials without shearing. Later, the pumps gained popularity in the food industry. The pumps can safely handle:
- Emulsions, inks, adhesives and resins in the chemical industry
- Crude oil, waste oils and many different types of traditional or alternative fuels in the petroleum markets
- Molasses, cooking oil, cocoa butter and other food industry-related materials
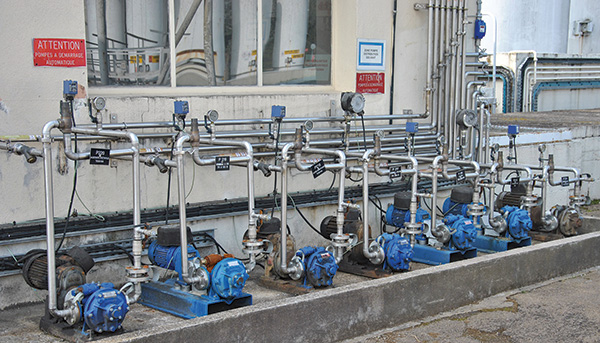
While this technology has forged an acknowledged reputation for durability in these markets, that reputation remained mostly unknown outside Western Europe for many years. However, with time, word spread about the value of this technology in many applications. As commerce traditionally dictates, supply eventually needed to meet growing global demand.
The eccentric disc pumping technology is the vision of French engineer Andre Petit, who worked in gold mines. When he examined the prevailing processes for transferring water and other liquids from the mine, he set out to improve them and invented eccentric disc technology for pump operations in 1906. However, Petit first needed to improve on existing pump design inefficiencies.
Fixing Design Inefficiencies
Part of Petit’s motivation to improve fluid transfer in mining operations centered on the inefficiencies of the two prominent pump technologies during the time: internal gear pumps and lobe pumps. Specifically, he noted that gear pumps’ style of operation left them susceptible to decreased flow capacity. This starts with the meshing of the gears, which pump fluids by displacement, forcing the gears to contact each other as they turn. This contact causes the gears to wear, resulting in increased clearances between the gear teeth, which leads to a loss of volumetric consistency. As they wear, gear pumps are also forced to run at higher speeds to maintain desired flow rates. The overall result is decreased performance and reliability with a corresponding increase in operating and maintenance costs.
Lobe pumps may offer continuous flow, run-dry capabilities and the ability to handle a wide range of liquids, solids and slurries, but they wear constantly because of design deficiencies. When a lobe pump wears, the internal clearances increase, resulting in reduced flow capacity and volumetric consistency over time, along with an increase in efficiency-robbing product slip.
Lobe pumps also feature two shafts that must be sealed, which doubles the potential for leakage. Lobe pumps must operate at decreased speeds to handle high-viscosity liquids and can deliver poor performance when handling low-viscosity liquids.
Recognizing the inherent deficiencies in the operation of gear and lobe pumps, Petit planned to create a pumping technology that remedied these design shortcomings. His innovation would become an important component in manufacturing and liquid-handling in many global industries.
Sustainable Innovation
In Petit’s design, eccentric disc pumps feature a disc that is placed inside a pump cylinder. The disc is driven by an eccentric bearing installed on the pump shaft. This creates two distinct pumping chambers that increase and decrease in volume as the eccentric bearing moves the disc, producing suction and discharge pressures as the chambers move in pairs that are 180 degrees apart. This ensures that the fluid passes through the pump at a constant flow rate.
During operation, the pump’s disc is driven by the eccentric movement of the shaft, which allows products to flow through the pump’s inner and outer chambers. This eliminates any possibility of pulsation within the pumped liquid and any slip is negligible.

In contrast with other pump technologies, the eccentric disc design enables self-priming, which ensures strong suction even after the pump runs dry. When other pumps run dry, they continue to operate even after the material has been transferred to clear the lines. As a result, the pump’s components can potentially burn and seize, resulting in costly damage to the pump internals. Eccentric disc pumps, by comparison, have the ability to run dry for a limited time without the risk of pump damage.
The eccentric disc design also ensures gentle product handling with low shearing and has the ability to self-compensate for mechanical wear, guaranteeing consistent flow rates over time. Petit’s eccentric disc pump design features high vacuum and compression effects for strong line-stripping ability and a reduced number of components for quick and easy disassembly and reassembly. The eccentric disc principle allows these pumps to continually run in reverse, which enables the back pumping of liquids.
International Expansion
While eccentric disc pumps offered the gentle handling, reliability and operational efficiency needed on a global landscape, the technology remained relatively unknown outside Europe. Launched in 1965, a series of eccentric disc pumps quickly built a reputation for robustness, delivering up to 40 years of virtually maintenance-free service in some of the most demanding applications in the chemical, food and oil industries. For years, the pumps remained a Western European technology. Technological advancements in evolving industrial applications necessitated design enhancements, and those design enhancements have enabled the pumps to enter the international market.
Modernization
To prepare these pumps for use in global markets, a critical modification was made to the pumps’ flanges. Previously only available with non-standardized flanges, their new design was equipped with ISO PN16/ANSI 150 flanges. Using flanges certified by the International Organization for Standardization (ISO) and American National Standards Institute (ANSI) enables the pumps to meet all applicable global operating standards.
Another critical part was the pumps’ mechanical seals. The mechanical seal is positioned behind the piston to provide shaft sealing. Previously, operators could only use the pumps with specific mechanical seals, but they can now be equipped with standardized seals. This helps expedite installations because end users no longer have to wait for the delivery of specialized seals.
From a performance perspective, the redesigned pumps have doubled their maximum differential pressure from 5 bar (73 psi) to 10 bar (145 psi), allowing them to be used in many new applications. The pumps are now available in ductile-iron construction. Previously, they were available in cast-iron construction only. This material enhancement is critical because more companies in the petrochemical industry are moving away from cast-iron construction.
The redesigned pumps enable product transfer up to 150 C (302 F) and the use of heating or cooling jackets with products that can solidify at ambient temperatures. The pumps are ATEX-certified and can run dry for up to three minutes in potentially explosive environments.
Conclusion
True greatness can be achieved by pursuing a dream that no one else can see. Andre Petit chose to pursue greatness and designed the eccentric disc principle in pump operations, a technological development that provides efficiency, reliability and durability. The technology improves end users’ liquid-handling operations and gives them peace of mind.